沖壓起皺因素及解決方法
沖壓工藝的發(fā)展有效推動(dòng)了汽車行業(yè)的發(fā)展,但是在沖壓件生產(chǎn)的過程中,經(jīng)常遇到的問題就是沖壓件起皺.出現(xiàn)這種情況會(huì)導(dǎo)致較為嚴(yán)重的后果。
影響沖壓件起皺因素
(1)拉伸深度影響
材料流動(dòng)阻力沿凹模口的分布于拉伸深度有直接的關(guān)系。在內(nèi)凹和外凸的曲線位置上,拉伸深度過大能引起變形阻力的不均勻分布,形成起皺,應(yīng)盡量避免。
(2)調(diào)整壓邊力的大小
當(dāng)皺紋在制件四周均勻產(chǎn)生時(shí),應(yīng)判定為壓料力不足,逐漸加大壓料力即可消除皺紋。當(dāng)拉伸錐形件和半球形件時(shí),拉伸開始時(shí)大部分材料處于懸空狀態(tài)。輕易產(chǎn)生側(cè)壁起皺,故除增加壓邊力外,還應(yīng)采用增加撿伸筋來增大板內(nèi)徑向拉應(yīng)力,消除皺紋。
(3)凹模圓角的半徑影響
凹模的圓角半徑過大,毛坯向凹模內(nèi)流動(dòng)經(jīng)過凹模圓角是產(chǎn)生彎曲變形的彎曲阻力越小。彎曲阻力越小,越容易造成起皺的發(fā)生。凹模半徑小彎曲變形的彎曲阻力越大,越不容易起皺,但易造成制件的開裂和拉毛現(xiàn)象產(chǎn)生。
通過大量的生產(chǎn)實(shí)踐經(jīng)驗(yàn)積累證明,沖壓件的起皺的主要原因,為拉伸過程中材料的堆積和局部材料運(yùn)動(dòng)速度的過快造成的。在制定實(shí)際解決方案時(shí),應(yīng)從以上方面考慮調(diào)整模具的相應(yīng)機(jī)構(gòu),會(huì)取得不錯(cuò)的效果。
拉伸件起皺的原因分析
拉伸件在拉伸過程中起皺的原因很多,主要原因有以下幾個(gè)方面:
(1)沖壓件拉伸深度太深,導(dǎo)致制件在走料的過程中板料流動(dòng)過快,形成起皺。
(2)沖壓件在拉伸過程中凹模R角過大,導(dǎo)致在拉伸過程中凸模無法壓住料,造成板料流動(dòng)過快形成起皺。
(3)沖壓件壓料筋不合理,壓料筋過小和位置不正確,不能有效阻止板料過快流動(dòng),形成起皺。
無壓料筋起皺明顯
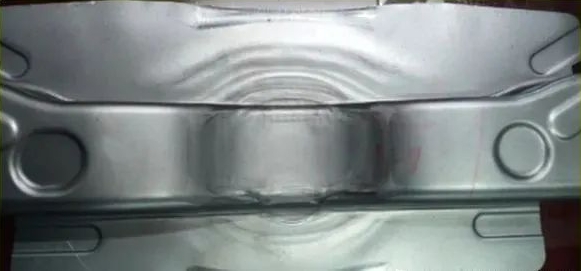
有壓料筋效果明顯提升
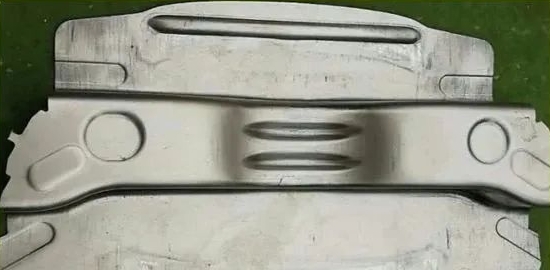
(4)頂桿的壓力過小,使沖壓件成型不徹底,形成起皺。
(5)模具定位設(shè)計(jì)不合理,導(dǎo)致沖壓件拉伸過程中無法壓住料或者壓料邊過小,導(dǎo)致在拉伸過程中無法壓住料,造成起皺。
(6)凸凹模間隙過大導(dǎo)致在拉伸過程中無法壓住料,造成起皺?;蛘邏毫厦骈g隙不合適出現(xiàn)“里松外緊”問題。
防止沖壓件起皺的措施方法
防止起皺的方法就是要保證五金沖壓件在拉伸過程中模具能夠壓住料,保證合理的板料流動(dòng)速度。沖壓件在拉伸時(shí)板料流動(dòng)過快,則可造成起皺;另一方面,板料流動(dòng)過慢,則可造成沖壓件開裂。
(1)采用合理的壓料裝置
當(dāng)采用壓料裝置時(shí),壓料裝置將毛坯變形部分緊緊壓在,并對(duì)其作用壓料力,以防止凸緣部分拱起而造成起皺。壓料力的大小要合適。壓料裝置分為彈性壓料和剛性壓料兩類。彈性裝置適用于淺拉深,剛性裝置適用于深拉伸。
(2)合理采用拉延筋
在壓料面上設(shè)置拉延筋是調(diào)節(jié)控制變形阻力的一種有效和使用的方法。拉延筋能夠很好的調(diào)節(jié)材料的流動(dòng)情況,使拉伸過程中各部分的材料流動(dòng)阻力均勻,使材料流入到型腔中的量適合制件的需要,防止多則起皺,少則開裂的現(xiàn)象。對(duì)于形狀復(fù)雜的曲面拉伸件,尤其是凸緣較小的拉伸件,應(yīng)設(shè)置拉延筋,以提高拉伸的徑向拉應(yīng)力以控制起皺;拉延筋的設(shè)置位置在徑向拉應(yīng)力較小的部位上,即板料易流動(dòng)的部位。對(duì)于凸緣較小的零件,為了設(shè)置拉延筋,可適當(dāng)增加一些材料(工藝補(bǔ)充材料),修邊時(shí)再將這部分去除掉。對(duì)于拉伸深度相差大的拉延件,拉延筋應(yīng)設(shè)置在進(jìn)料少的部位,這樣就可組織該部分過多的材料拉人凹模腔內(nèi),從而防止起皺。
以上為沖壓件拉伸過程中起皺的常見原因,在具體問題中需要具體的分析。根據(jù)沖壓件的具體情況來查找具體的原因。
來源:網(wǎng)絡(luò)